Flownex Simulation Environment 2024 v8.16.0.5519
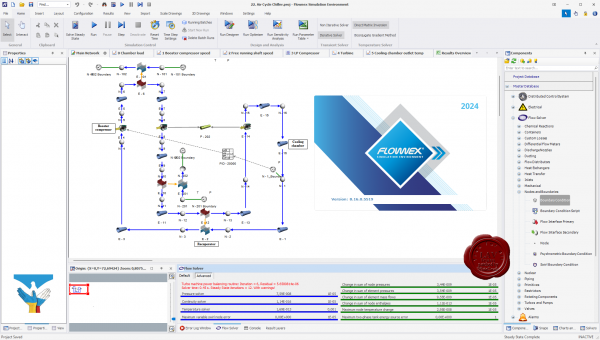
Flownex Simulation Environment delivers technology that enables you to study how systems will behave in the real world, where fluid is the driving factor. Flownex system simulation relays the overall effect of changing specific properties on components, allowing clients to examine extensively all possible variations of a system in the design and optimization of systems.
Flownex Simulation Environment provides turbomachinery engineers with an easy to use, off-the-shelf tool for modelling combustion chambers, secondary air systems, blade cooling flows, lubrication systems with oil-air mixtures, as well as overall cycle integration and operation.
Blade Cooling
By coupling 1D flow Flownex models with 3D heat transfer models in ANSYS Mechanical or CFX, a detailed turbine blade cooling simulation can be conducted. Flownex contains industry-standard pressure drop and heat transfer correlations for typical turbine blade features such as turbulator strips and pedestals. This allows designers to rapidly see the effects of their design changes on the maximum blade temperatures and cooling airflow rate.
COMBUSTION CHAMBER
Preliminary combustor design requires that an extensive number of geometrical and operational conditions be evaluated and compared. Especially during this phase, Flownex is an essential tool for combustor design engineers as it accurately captures important parameters such as the mass flow rate distribution through air admission holes, associated pressure losses as well as liner wall temperatures. Networks can be easily configured and solved within a few seconds. This result in substantial development cost savings because of the reduction in the number of detailed 3D simulations and rig tests required. A further advantage is the ability to use the Flownex results as boundary conditions for subsequent localized 3D models.
LUBRICATION SYSTEM
The primary use of Flownex in lubrication systems is used to determine optimum drain line sizes given the limited space inside the engine. This requires two-phase pressure drop calculations in lines with oil-air mixtures. In parallel with this engineers can determine whether or not scavenge pumps are required for fluid transportation in the drain lines and, if so, what the pumping requirement will be.
SECONDARY & COOLANT FLOW
Flownex includes a comprehensive rotating component library for analysing the secondary air system of a gas turbine engine. This enables engineers to quantify the bleed air consumption and flow distribution through the entire system. Furthermore, coupling Flownex with Ansys Mechanical enables engineers to perform detailed thermal studies of critical rotating components. Flownex includes:
- Real gas models.
- Windage power calculation.
- Choking calculations.
- User-defined HTCs.
Release notes